LED strip lights, a versatile and efficient form of lighting, have gained immense popularity in both residential and commercial spaces. This article, enriched with insights into the role of an LED strip light manufacturer, will explore the process of LED strip manufacturing, highlighting the intricate journey from concept to completion.
Design and Prototyping
Concept
The development of LED strip lights starts with a concept phase, which may originate from the manufacturer or arise from specific customer requirements. In this phase, a collaborative team consisting of engineers, designers, sales personnel, and customers comes together to define the essential features of the strip lights. These features include LED intensity, color spectrum, brightness, and energy efficiency. This stage is vital in establishing a solid foundation for a product that is not only high in quality but also functional.
Involving a diverse team in the conceptualization process is crucial. Sales staff and customers provide valuable insights into market trends and individual client preferences. This collaborative approach ensures that the final product not only meets technical specifications but also aligns with market demands and specific needs of clients, ultimately enhancing the practicality and appeal of the LED strip lights.
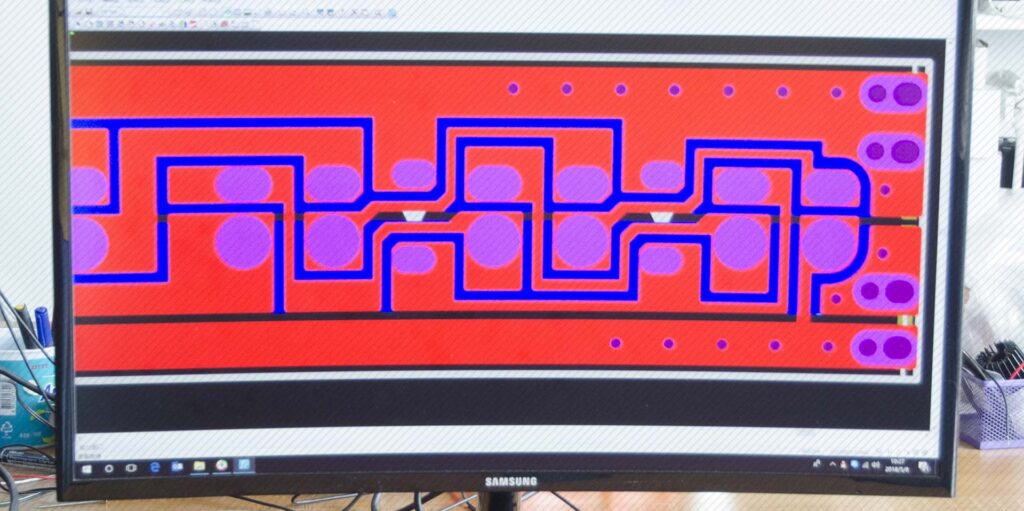
Prototype Development
Once the concept of the LED strip light is finalized, the prototype development phase begins. In this phase, engineers craft a working model, providing a tangible representation of the initial concept. This prototype is crucial for designers and engineers to test and refine the product's features. It's a period marked by trial and error, allowing for adjustments to perfect the design before proceeding to mass production.
The prototype is subjected to rigorous and extensive testing to meet high-quality standards and desired specifications. Tests include an electric test to assess electrical safety and functionality, a max run length test to determine the strip's optimal operating length, and spectrum tests to verify color temperature and color rendering index (CRI). Additionally, photometric testing is conducted to ensure the light output is consistent and meets the required performance criteria.
Materials and Components
LED Chips
At the core of every LED strip light are the LED chips, tiny yet powerful components crucial for light production. The selection of these chips is pivotal, as it determines the brightness, color accuracy, and energy efficiency of the strip.
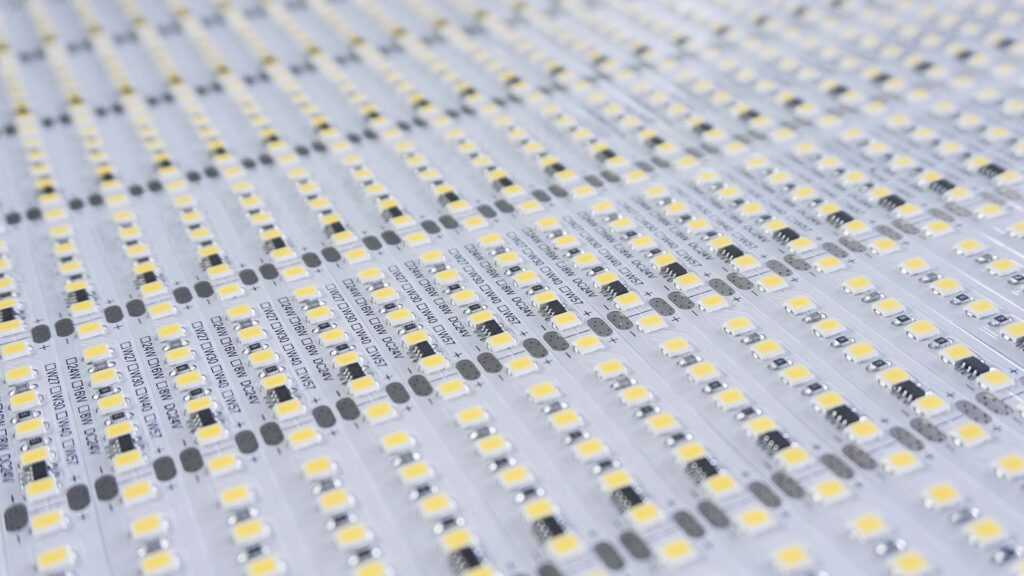
LED strips typically utilize Surface-Mounted Device (SMD) LEDs, valued for their compact size and efficiency. The choice among different SMD types, such as SMD 5050, 2835, 3528, 3014, 3020, 5730, 3030, and 4040, depends on the required brightness and color capabilities. For example, SMD 5050 chips can house four diode chips, enabling RGB and RGBW color mixing, while SMD 2835, known for its efficiency, is suited for single-color applications. SMD 3528 offers a balance in size and brightness, ideal for moderate lighting needs. SMD 3014 and 3020 are smaller, offering high brightness in a compact form. SMD 5730 is known for its high efficiency and brightness, suitable for applications requiring intense illumination. SMD 3030 is known for its high lumen output in a small package, and 4040 provides enhanced thermal performance and light quality for more demanding applications.
Key aspects in the selection of LED chips include:
- Bin Selection: LEDs are chosen from specific manufacturing bins, and categorized based on color temperature and brightness, to ensure uniformity across the strip.
- Forward Voltage and Current: The forward voltage and operating current of each LED chip are essential factors in determining the strip's power requirements and the design of its current control circuitry.
Moreover, the quality of the LED chip is paramount. Renowned brands like Bridgelux, Samsung, Cree, Osram, Nichia, and several local Chinese brands are recognized for producing high-quality LED chips. These Chinese local brands offer advantages such as fast delivery, flexibility, and the ability to custom-tailor special color temperatures like 1800K, 2300K, and 2500K for various applications. Their quality is guaranteed, with some of these brands being foundries for other renowned brands. Collectively, these brands deliver superior luminosity and color consistency, significantly enhancing the performance and application range of the LED strip lights.
PCB
Flexible PCB
The Printed Circuit Board (PCB) is a crucial component of LED strip lights, acting as the mounting surface for LED chips and other electronic elements. Its design and quality significantly impact the strip's flexibility, heat dissipation, and durability.
- Material Composition: Typically made from materials like polyimide or polyester, these PCBs offer the needed flexibility for versatile applications, allowing the strip to bend without damage.
- Thickness and Flexibility: The thickness, usually between 0.1mm and 0.2mm, is selected to balance flexibility with heat dissipation, a key factor in the longevity and functionality of the LED strip.
- PCB Layout and Design: The layout is designed for even electrical current distribution, with copper conductors optimized to minimize voltage drop and maintain uniform brightness. Complex designs might include multiple layers for intricate circuitry.
- Copper Thickness: The copper thickness in PCBs for LED strip lights is a critical factor for ensuring efficient electrical pathways and flexibility. Typically, this thickness is around 35µm, balancing conductivity and the ability to conform to different shapes. In more advanced designs, We, LinnLED, use two-layer copper configurations for enhanced performance:
- 3Oz (35um + 70um): Combining a standard 35µm layer with an additional 70µm layer, this configuration offers improved current capacity and heat dissipation, suitable for higher power LED strips.
- 4Oz (35um + 105um): This design features a 35µm layer coupled with a 105µm layer, totaling 140µm. It's ideal for applications requiring high power densities, superior thermal management, and long run.
Rigid PCB
In addition to flexible PCBs, rigid PCBs are also used in LED strip lights, particularly in applications where flexibility is not a requirement and structural stability is prioritized.
- Material and Structure: These PCBs are commonly made from fiberglass (FR4) or Metal Core Printed Circuit Boards (MCPCBs). Fiberglass offers a stable, durable base for LED components and is resilient during handling and installation. MCPCBs, typically aluminum or copper, provide superior heat dissipation, essential for high-power LED applications.
- Heat Dissipation: The thicker and more stable structure of rigid PCBs allows for better heat management, crucial in applications with high power requirements.
- Applications: Ideal for linear lighting solutions, such as under-cabinet lighting, where bending the strip is unnecessary. Their rigidity makes them well-suited for installations on flat surfaces.
- Design Considerations: Rigid PCBs can accommodate larger components and more complex circuitry, focusing on maximizing durability and electrical efficiency.
Both flexible and rigid PCBs play vital roles in the world of LED strip lights, each with its specific applications and advantages. Flexible PCBs offer versatility and adaptability, while rigid PCBs provide structural stability and enhanced heat dissipation for more demanding applications
Resistors, Current Regulators, and Other Components
LED strip lights incorporate several key components to ensure efficient and safe operation:
- Resistors: These are crucial for controlling the current flowing to the LEDs, thereby preventing overheating and extending their lifespan. The resistors are specifically chosen based on the LED's voltage and current requirements. Understanding the differences between various types of LED strips, including those using resistors, can be further explored in this detailed article: Differences Between Constant Voltage, Constant Current, and Constant Current Input LED Strip.
- Current Reglutors: ICs like current regulators, are essential components in LED strip lights. They serve to maintain a constant current across the strip, ensuring uniform brightness regardless of potential voltage drops.
- Controllers for RGB Strips: For strips capable of displaying multiple colors (RGB), controllers or specialized ICs, such as WS2812B (which combines an RGB LED with control circuitry), are included. These enable precise color control and programming.
Manufacturing Process
Assembling the PCB
The manufacturing of LED strip lights begins with a precise and technical assembly of the Printed Circuit Board (PCB).
- PCB Cutting: The process starts with cutting the PCB to the required lengths based on the specifications of the LED strip design.
- Copper Layer Application: A base layer of conductive copper is applied to the PCB, which is essential for forming the circuitry.
- Photolithography and Etching: The circuit pattern is transferred onto the copper layer using photolithography. Following this, precision etching is performed to remove excess copper, accurately creating the necessary circuit paths.
- Precision Etching for Fabrication: Further precision etching techniques are used to fine-tune the circuit patterns, ensuring accurate and consistent current flow essential for the strip's functionality.
This meticulous PCB assembly process lays the foundation for the reliable and efficient operation of LED strip lights, setting the stage for the subsequent steps in the manufacturing process.
Mounting LEDs
The mounting of LEDs onto the Printed Circuit Board (PCB) in the production of LED strip lights involves intricate technical processes and rigorous testing to ensure optimal performance and quality.
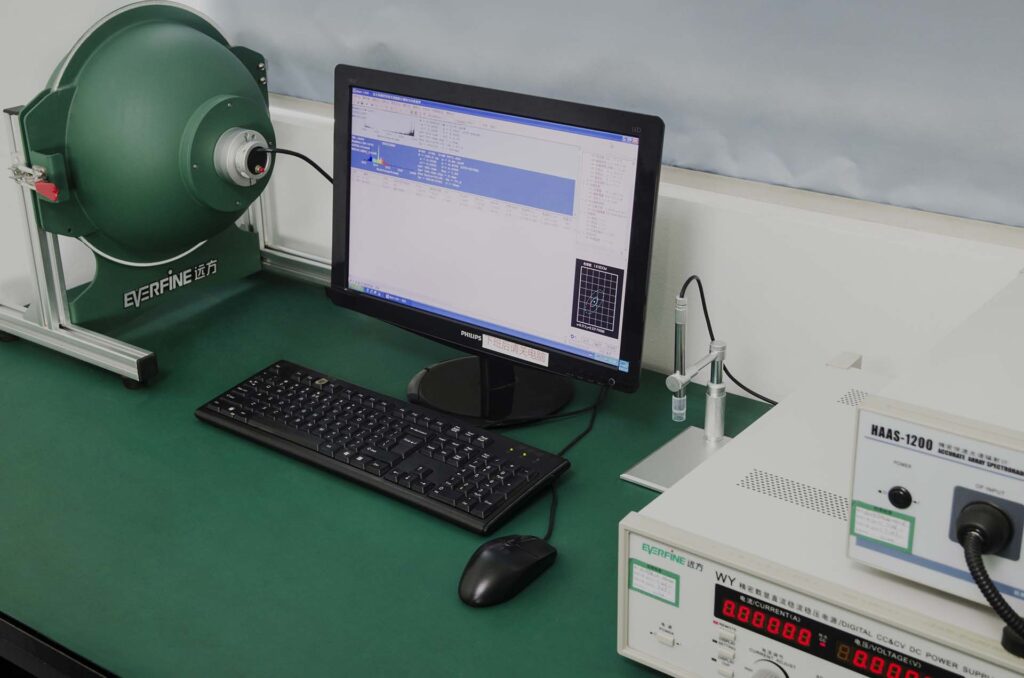
LED Testing Before Mounting
- Spectrum Testing: This test ensures color consistency and quality. It involves measuring the wavelength distribution of light emitted by the LEDs to verify that it meets specified color standards.
- Photometric Testing: LEDs undergo photometric testing to measure their luminous flux in lumens, verifying that they conform to the required brightness and efficacy standards.
Precision Placement Techniques
- Automated SMT Placement: Surface-Mount Technology (SMT) is employed for precise LED positioning on the PCB. Automated SMT machines accurately place each LED on designated solder pads.
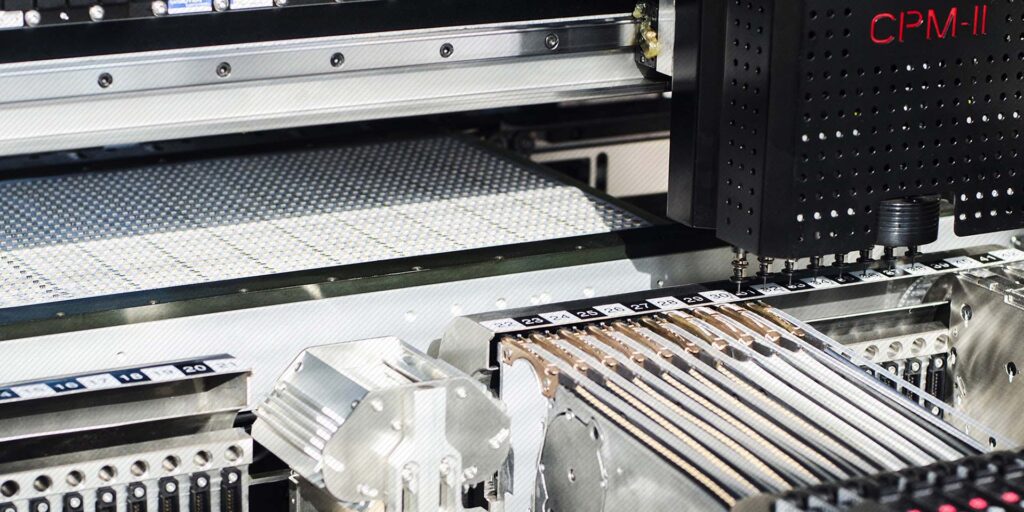
Soldering
Once the LEDs are mounted onto the Printed Circuit Board (PCB), the soldering process is initiated to establish robust electrical connections. This step is crucial for ensuring the longevity, structural integrity, and electrical functionality of the LED strip.
Reflow Soldering Technique
- Process Overview: The soldering of LEDs to the PCB is typically achieved through reflow soldering. In this process, the entire assembly, including the LEDs and PCB, is heated in a controlled environment. This controlled heating melts the solder, creating a strong bond between the LEDs and the PCB.
- Temperature Control: A key aspect of reflow soldering is the careful control of the temperature profile in the soldering oven. This precision ensures that the solder melts effectively without causing damage to the LEDs or the PCB.
- Ensuring Quality Bonds: The quality of the soldering directly impacts the strip's structural integrity and electrical stability. Properly executed reflow soldering ensures durable and stable connections, essential for the strip's overall reliability and performance.
The soldering stage in the production of LED strip lights is a critical component of the manufacturing process, securing the electrical pathways and reinforcing the physical structure of the strip.
Quality Control
Quality control in LED strip light manufacturing encompasses a series of precise and specialized tests to ensure each product meets high standards for performance, safety, and durability.
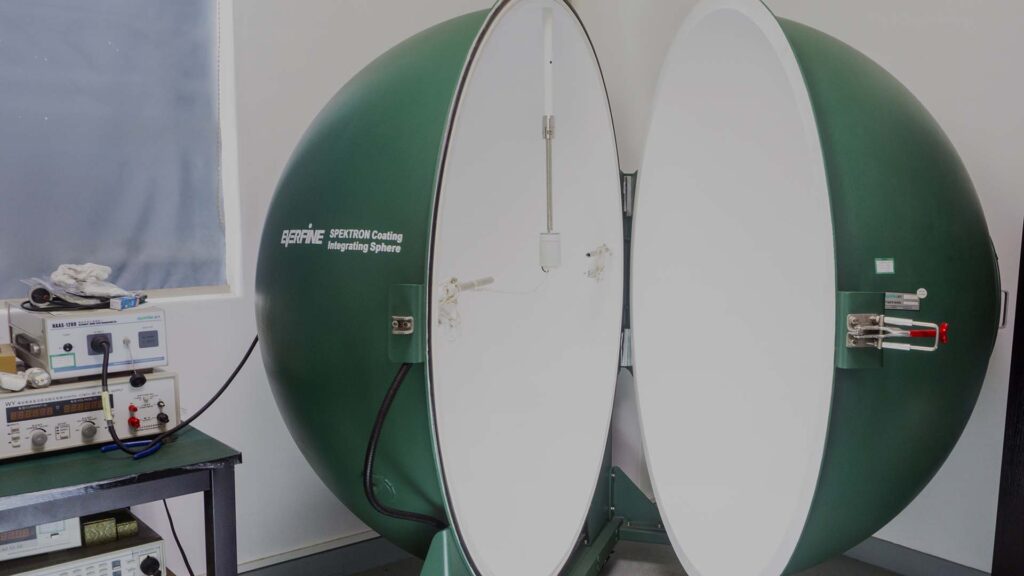
Detailed Testing Procedures
- Visual and Physical Inspection: Each strip is thoroughly examined for physical defects, including soldering accuracy and correct LED placement.
- Electrical Testing: This includes testing for voltage drop, power consumption, and current uniformity, alongside continuity and insulation checks to prevent short circuits.
- Spectrum (Integrating Sphere) Testing: This test, conducted using an integrating sphere, measures the spectral output and color properties of the LEDs, including luminous flux and color rendering index (CRI), ensuring consistent color quality and brightness.
- Photometer Testing: Focused on assessing the light's intensity and distribution, this test checks for uniformity across the strip and measures the luminous flux in lumens, verifying that they conform to the required brightness and efficacy standards.
- DALI Dimming Test: Digital Addressable Lighting Interface (DALI) dimming tests are conducted to evaluate the strip’s compatibility and performance with DALI dimming systems. This test is crucial for strips intended for use in smart lighting systems, ensuring smooth and precise dimming capabilities.
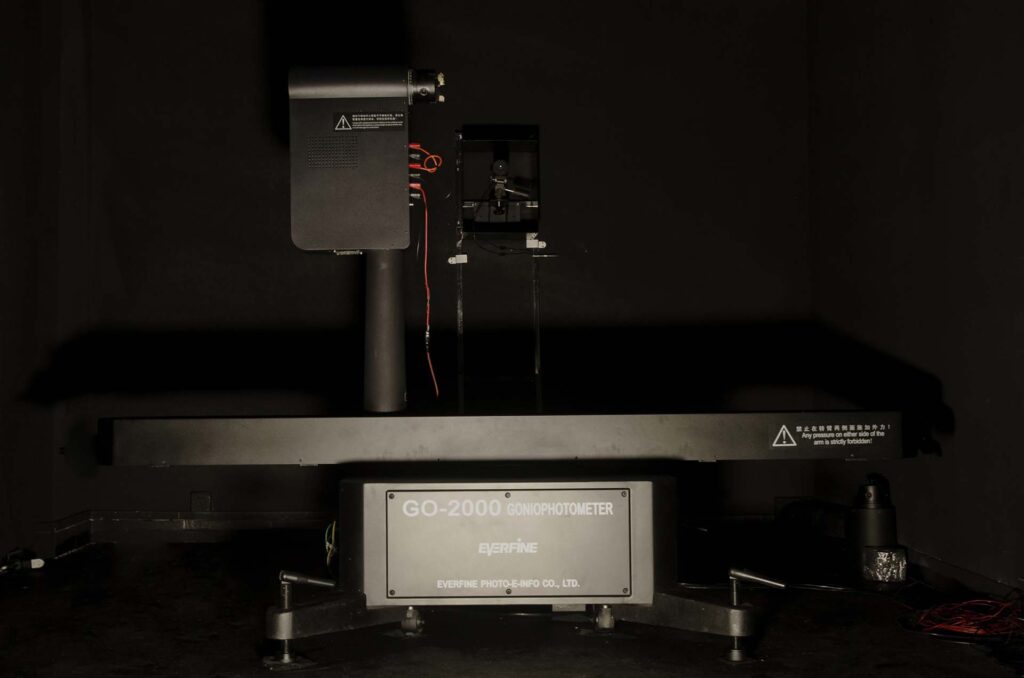
Longevity and Endurance Assessments
- Max Run Length Testing: Determines the longest effective operational length of the strip, assessing the limits before encountering voltage drops or overheating.
- Aging Test: Involves running the LED strip over extended periods to simulate long-term usage, identifying any potential issues in performance or early failures.
Each of these tests plays a vital role in the quality assurance process, combining detailed inspections with technical evaluations to ensure that the LED strips meet stringent industry standards. By conducting these specific tests, manufacturers ensure that their LED strip lights are reliable, efficient, and ready for various lighting applications.
Assembling Tape
After passing all quality checks, the LED strip lights are prepared for the final assembly step, which involves the application of adhesive tape for easy installation.
- Application of Adhesive Tape: The back of the strip is fitted with a high-strength, heat-resistant adhesive tape. This tape may be a heat-conducting adhesive or a specific high-quality option like 3M tape.
- Ease of Installation: The adhesive backing, whether heat-conducting or another type, is designed to make the installation of the strip lights straightforward and user-friendly, ensuring secure placement.
This application of adhesive tape marks the readiness of the LED strips for easy and efficient installation, underscoring the focus on convenience and performance in the product's design.
Packaging
Once the LED strips are manufactured and tested, they undergo a final stage of careful packaging, designed to ensure protection during transportation and to provide consumers with essential information.
- Reel Packing: The strips are typically wound around reels, facilitating easy handling and installation.
- ESD Protection: For strips with integrated circuits, Electrostatic Discharge (ESD) protective packaging is utilized to prevent any damage from static electricity.
- Anti-Static and Moisture Control: Each reel is encased in anti-static material, often accompanied by silica gel packets to control moisture. This safeguards the strips against potential damage during transit and storage.
Conclusion
The manufacturing process of LED strips is a testament to the collaboration between designers, engineers, and manufacturers, resulting in efficient, versatile, and high-quality lighting solutions. As technology advances, an LED strip light manufacturer continues to play a crucial role in innovating and refining these products, ensuring they remain integral to modern lighting applications.
FAQ
What are the key considerations when selecting LED chips for strip lights?
Factors include brightness, color accuracy, energy efficiency, and bin selection for uniformity in color temperature and brightness.
Why are different types of SMD LEDs used in LED strips?
Various SMD types like SMD 5050, 2835, 3528, and others are chosen based on required brightness, color capabilities, and specific applications.
How do resistors and current regulators affect LED strip lights?
These components control the current to the LEDs, preventing overheating and ensuring uniform brightness across the strip.
What tests are conducted during the prototype development phase?
Tests include electric safety, max run length, spectrum tests for color temperature, and photometric testing for light output consistency.
What is the importance of LED testing before mounting?
Spectrum and photometric testing ensure color consistency and brightness, verifying conformity to specified standards.
How is soldering conducted in LED strip light manufacturing?
The reflow soldering technique is used, where the assembly is heated in a controlled environment to melt the solder and create strong bonds.
What quality control tests are performed on LED strip lights?
Tests include visual inspection, electrical testing, spectrum testing, photometer testing, DALI dimming test, max run length testing, and aging tests.
How do flexible and rigid PCBs differ in LED strip lights?
Flexible PCBs offer adaptability for bending, while rigid PCBs provide stability and enhanced heat dissipation for high-power applications.
How does the selection of copper thickness in PCBs impact LED strips?
Copper thickness affects electrical pathways and flexibility, with thicker layers offering better current capacity and heat dissipation.
What are the advantages of using local Chinese brands for LED chips?
Benefits include fast delivery, flexibility, and custom color temperatures, with quality comparable to renowned brands.